Our Projects
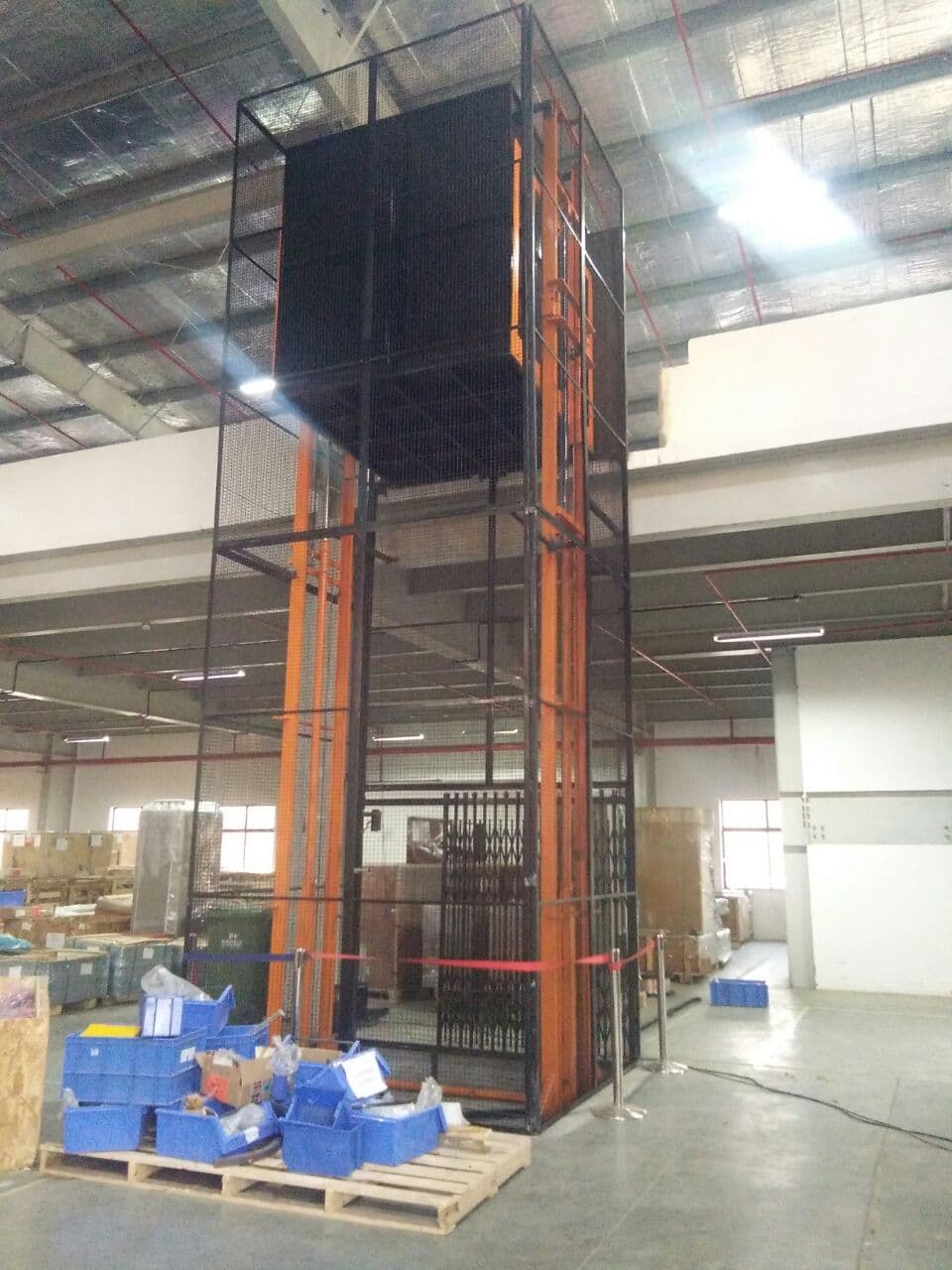
Goods Lift
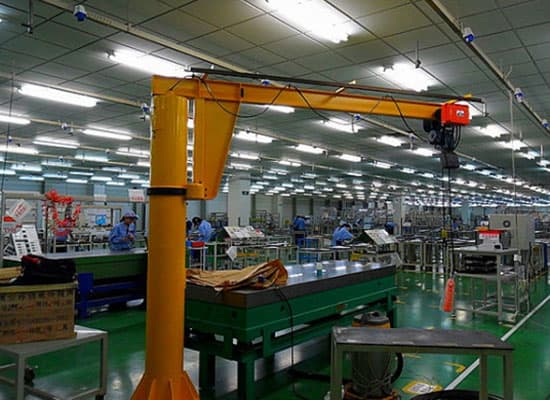
Jib Crane
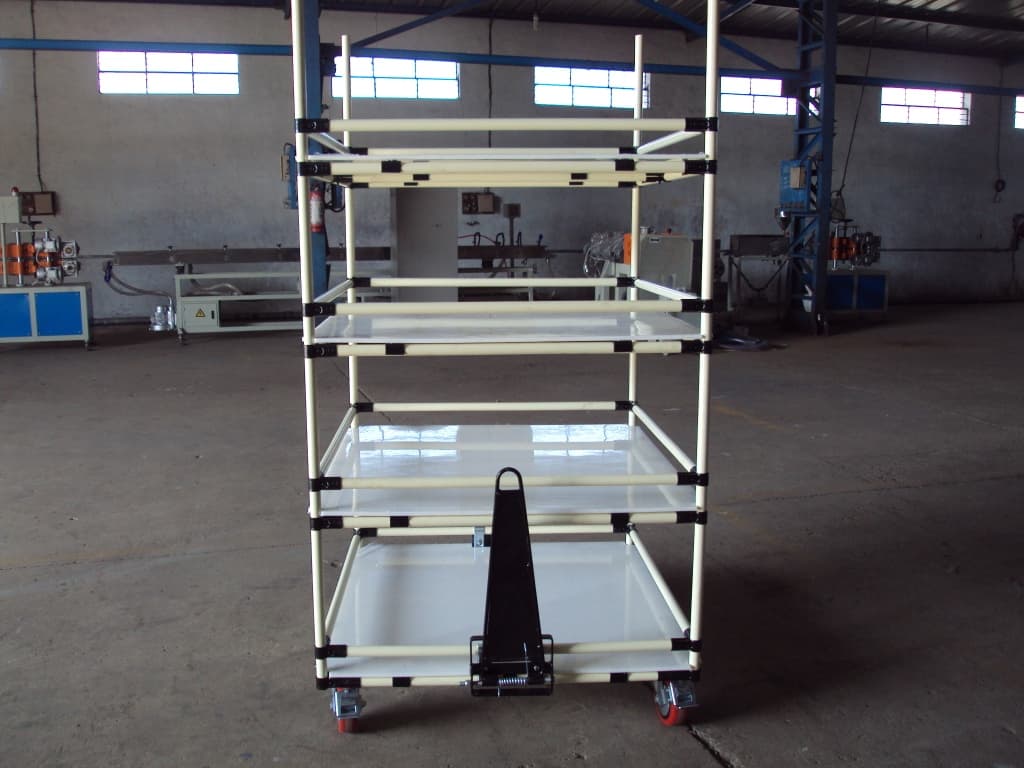
JLR Layer Trolley
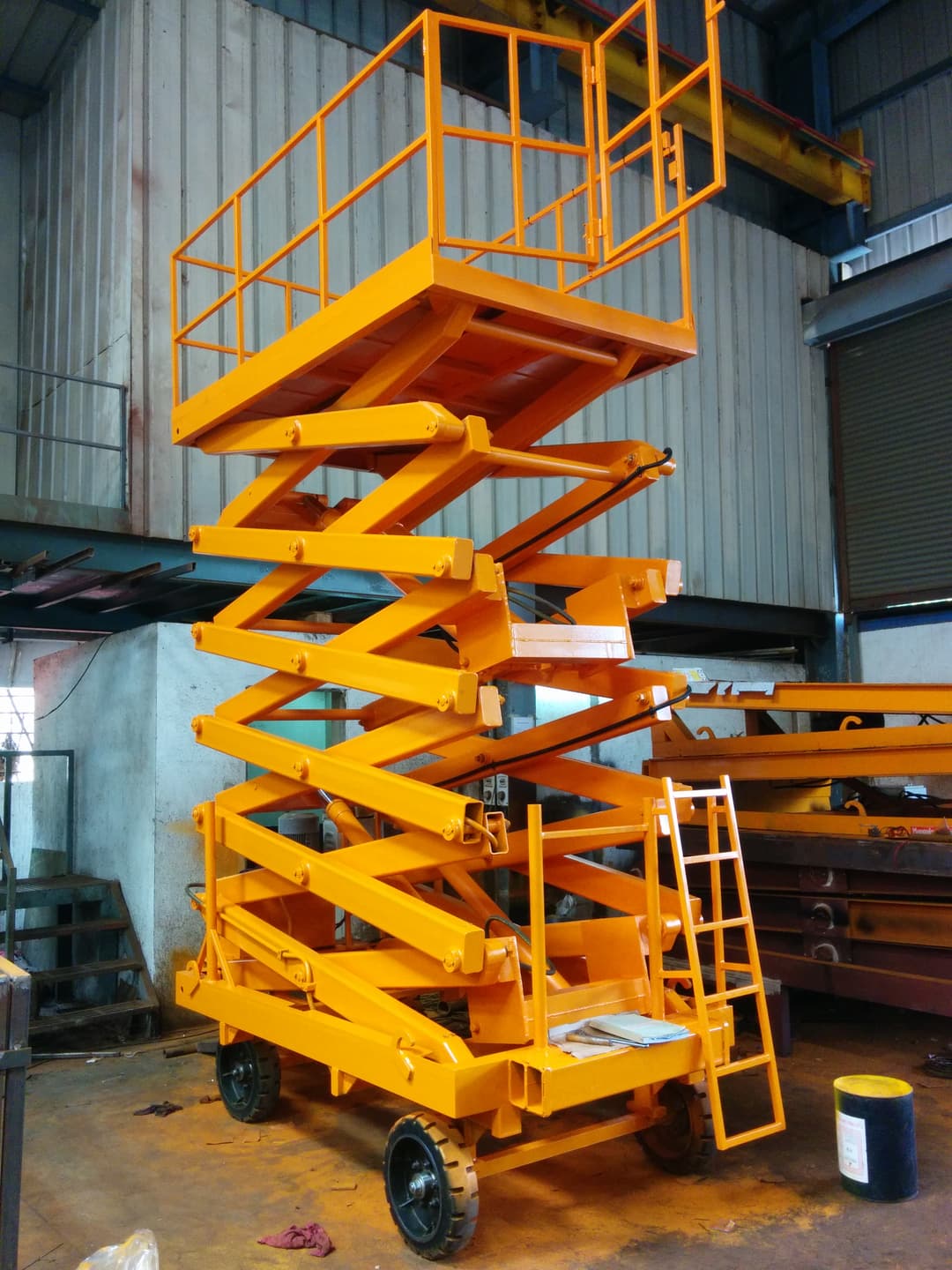
Mobile Scissor Lift
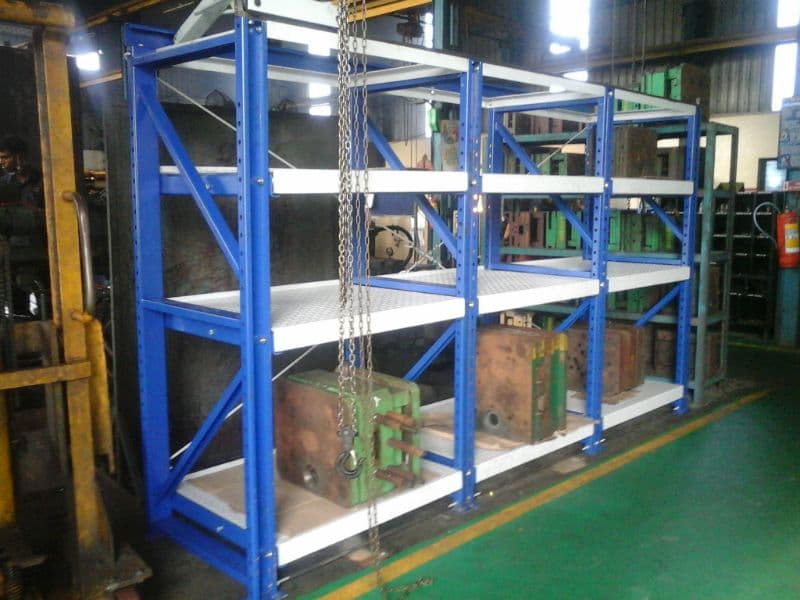
Mold Rack
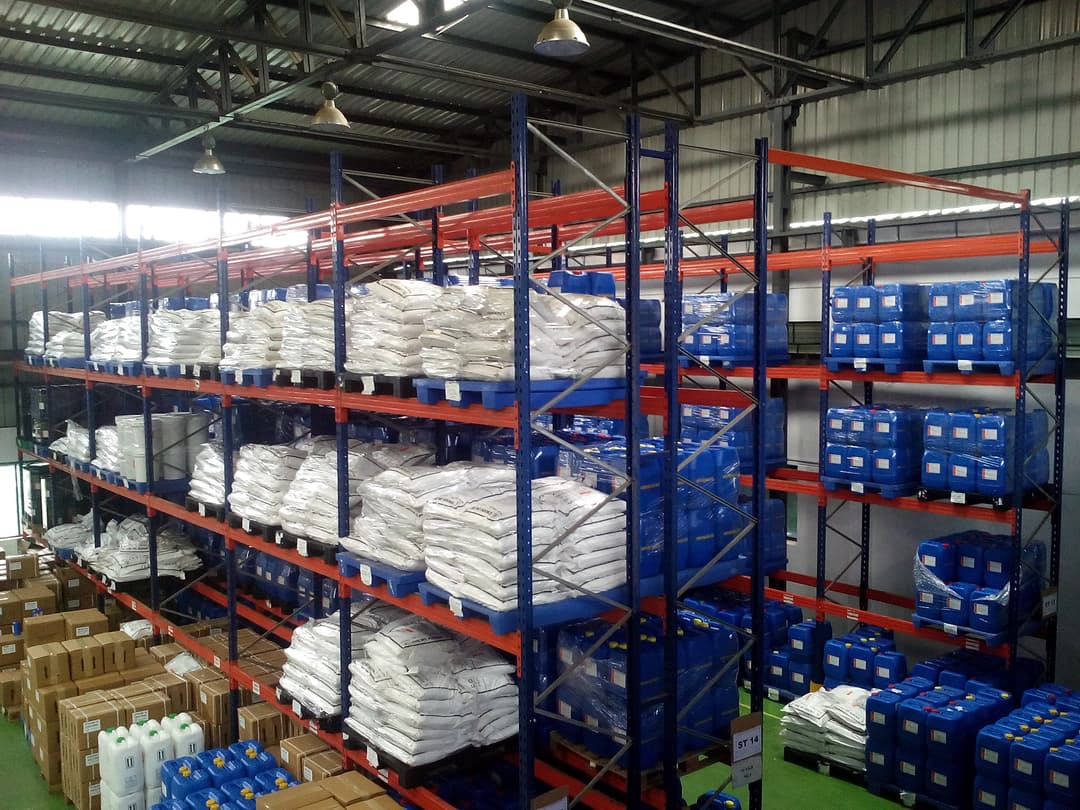
Pallet Storage Racks
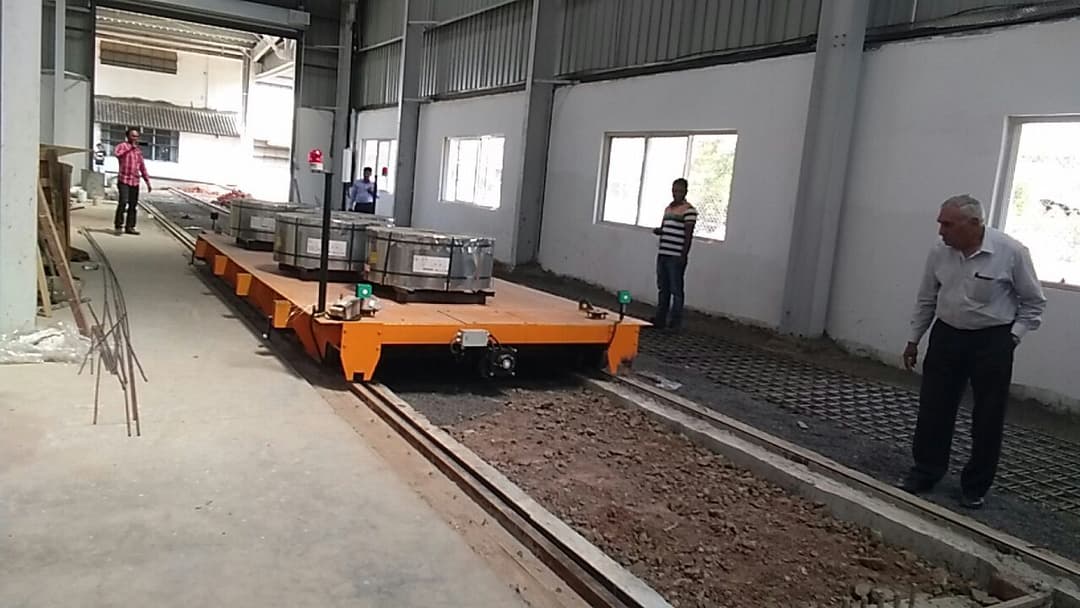
Rail Trolley
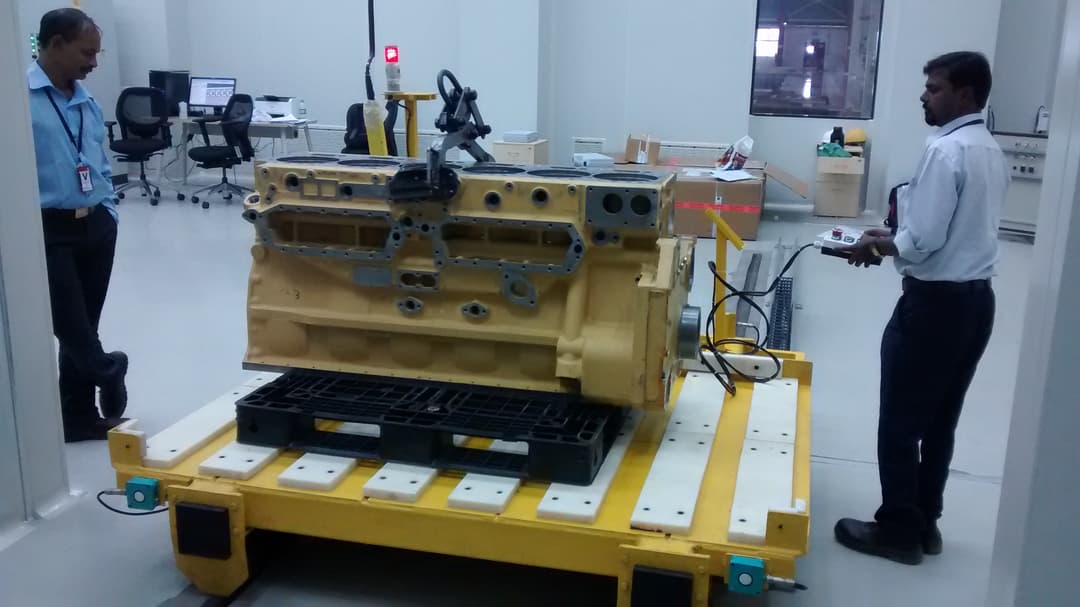
Rail Trolley
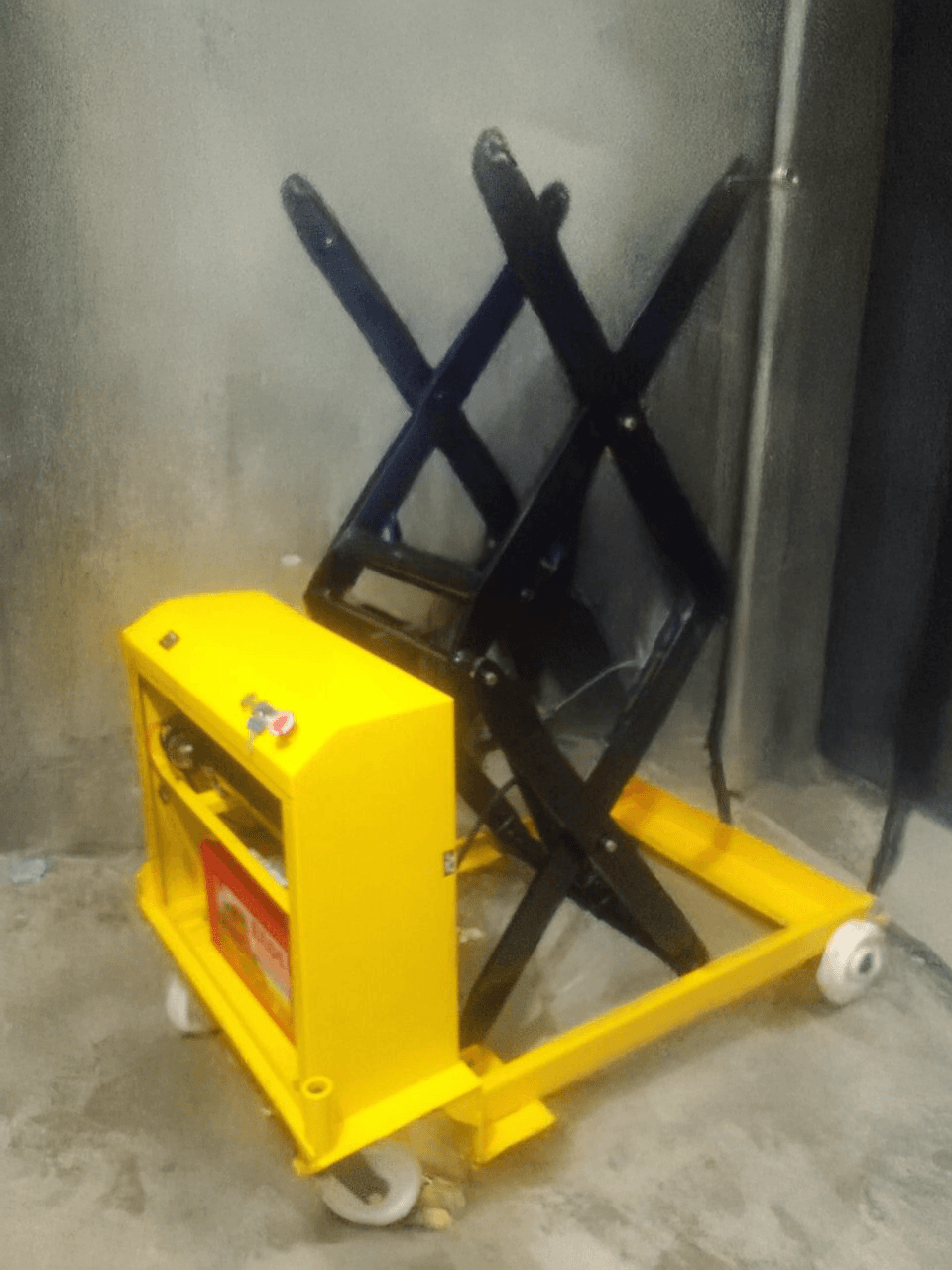
Scissor Lift
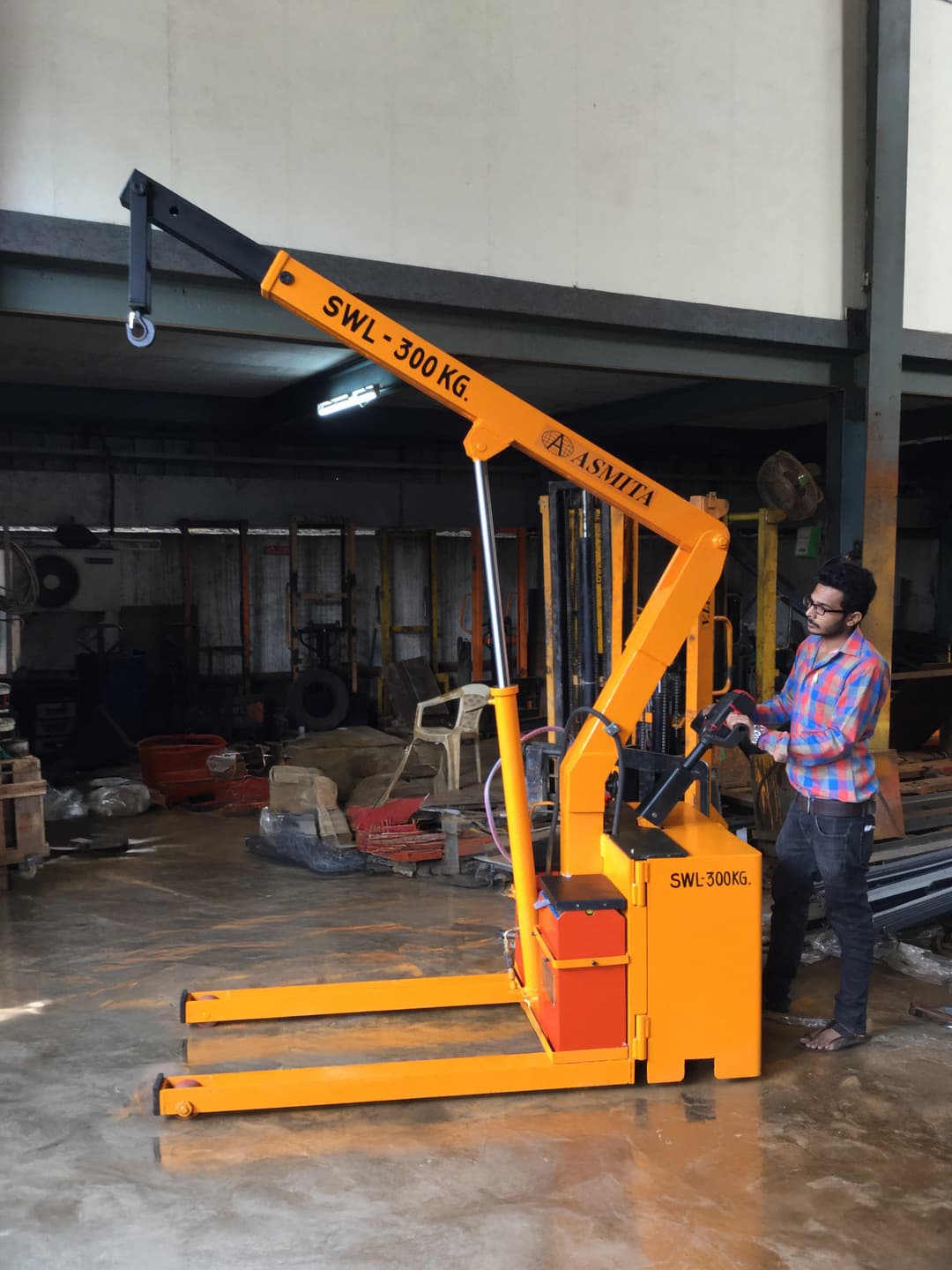
Shop Floor Crane
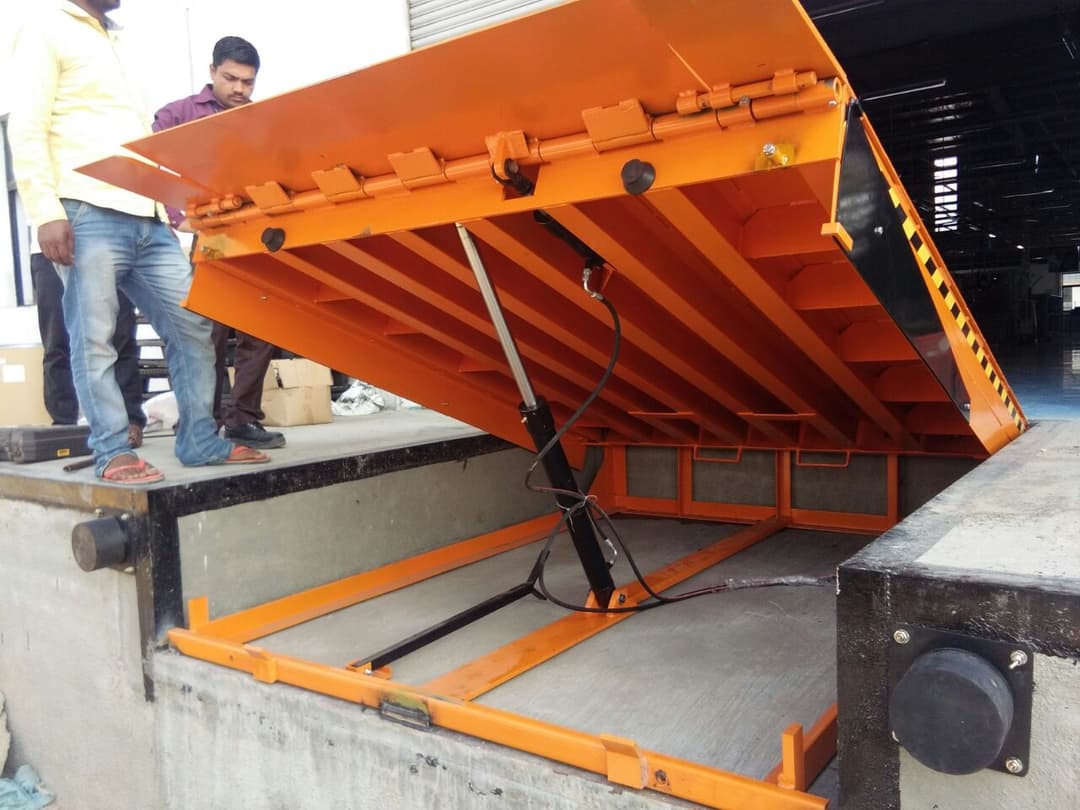
Dock Leveler
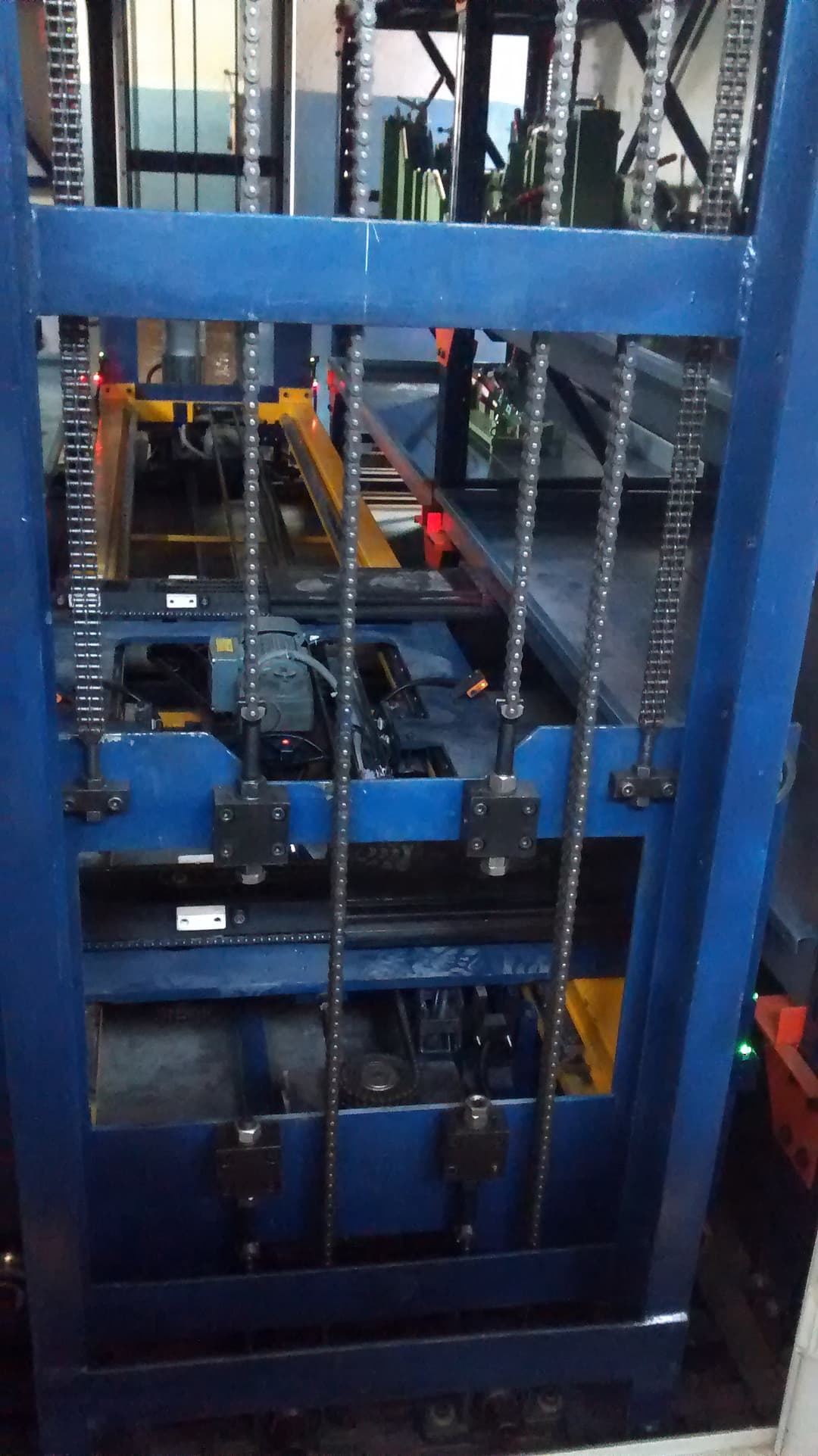
Automated Storage and Retrieval Systems
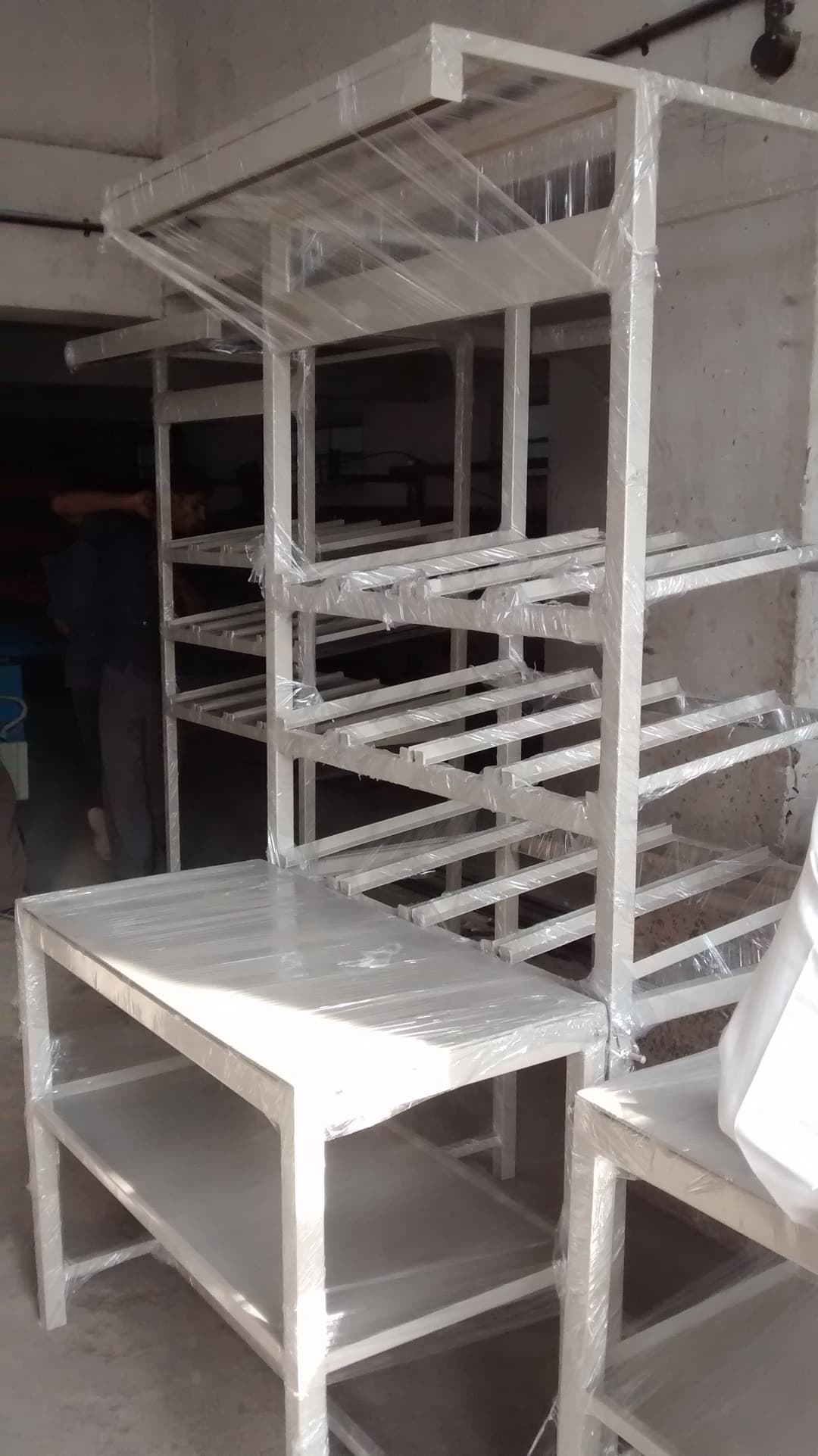
Work Station
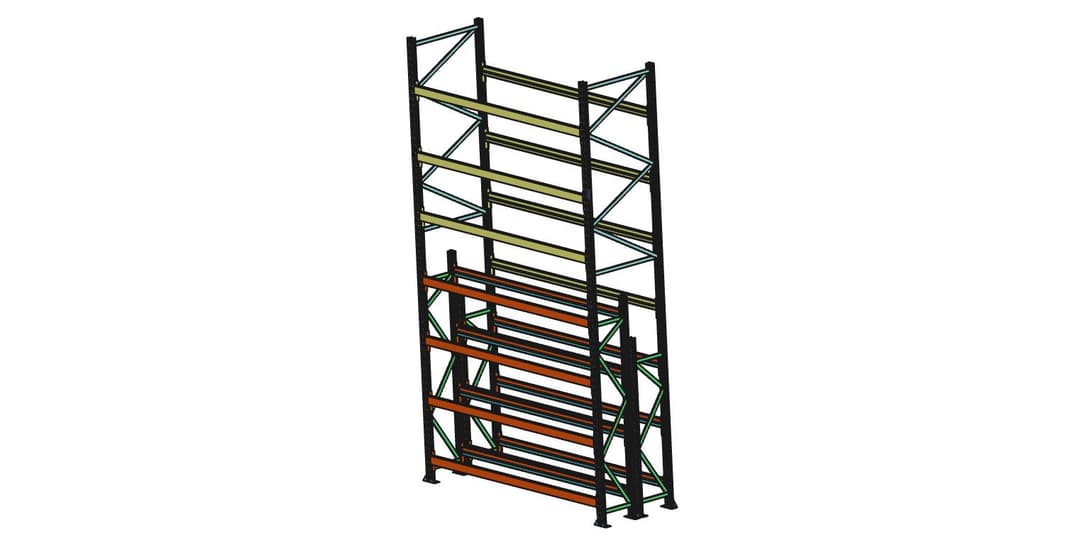
Complex Rack
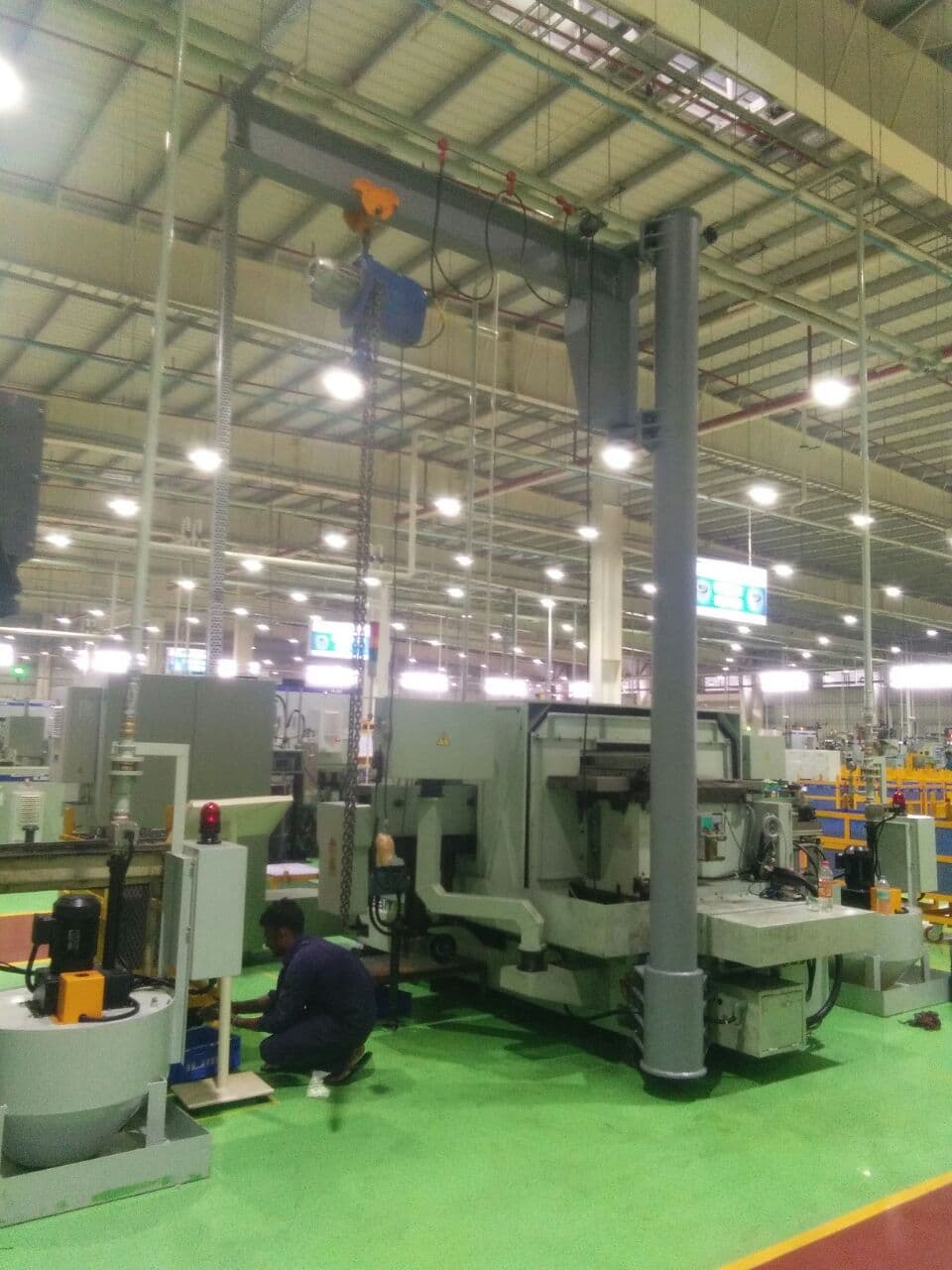
Crane - Jib
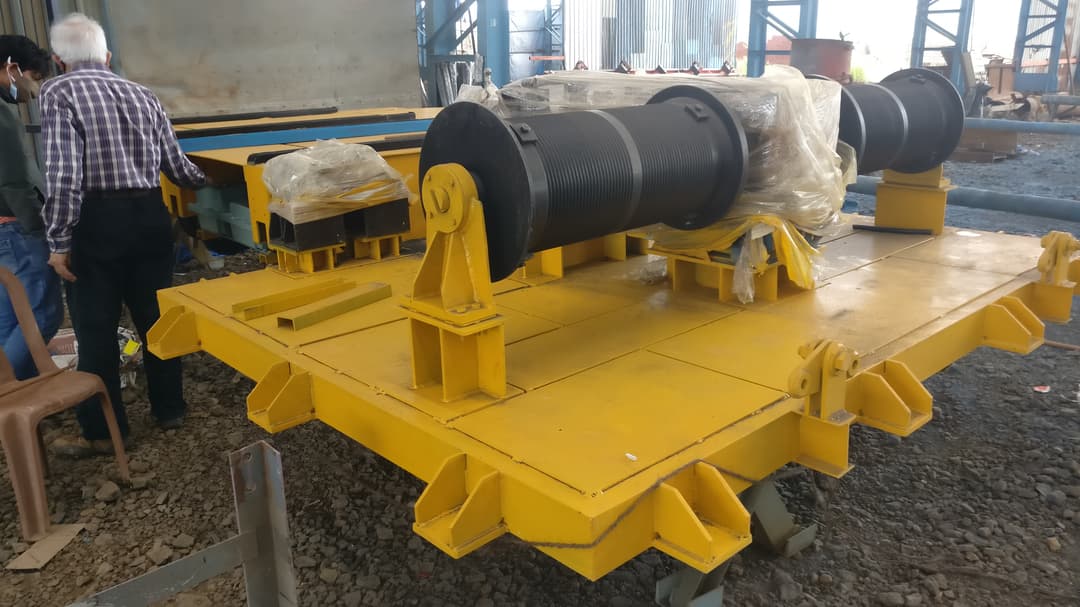
Goods Lift
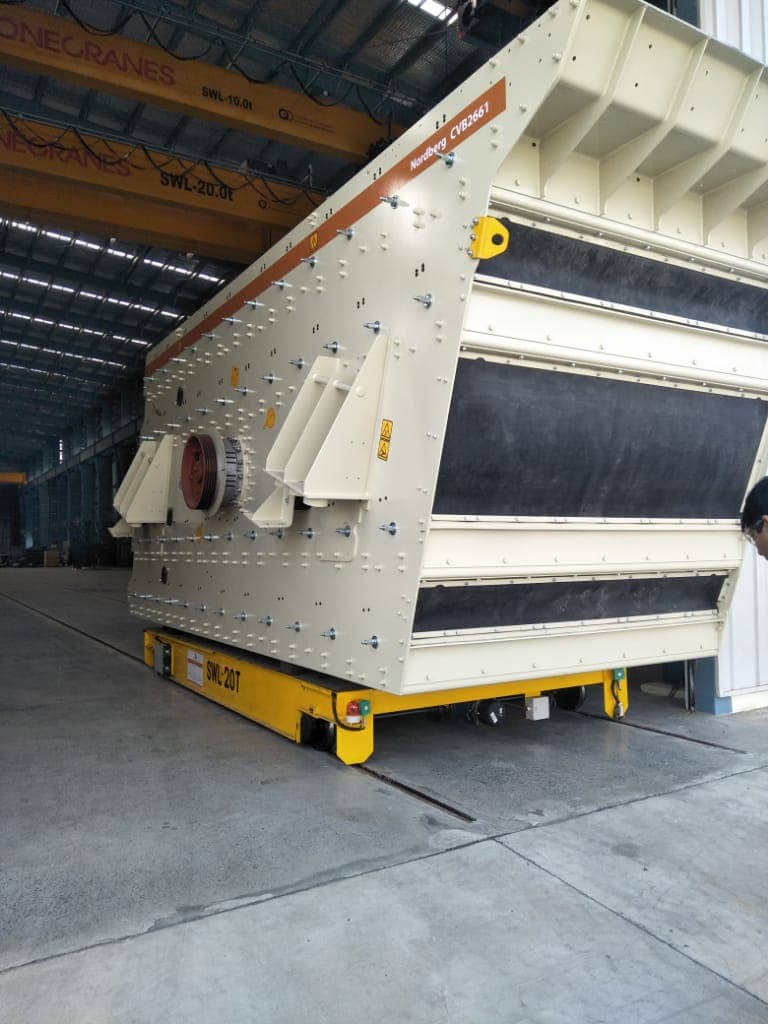
Motorised Trolly Battery Operated
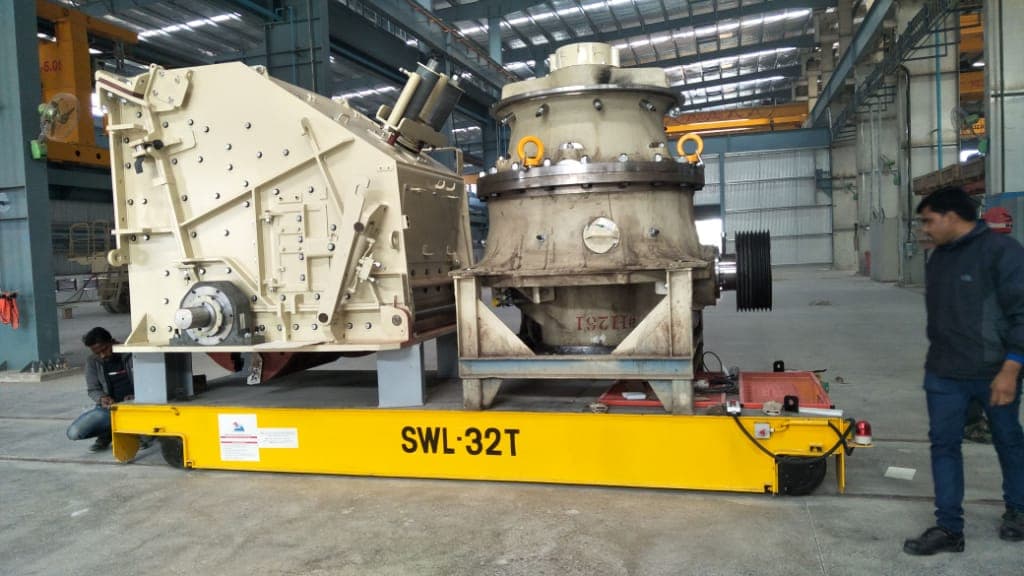
Motorised Trolly Battery Operated
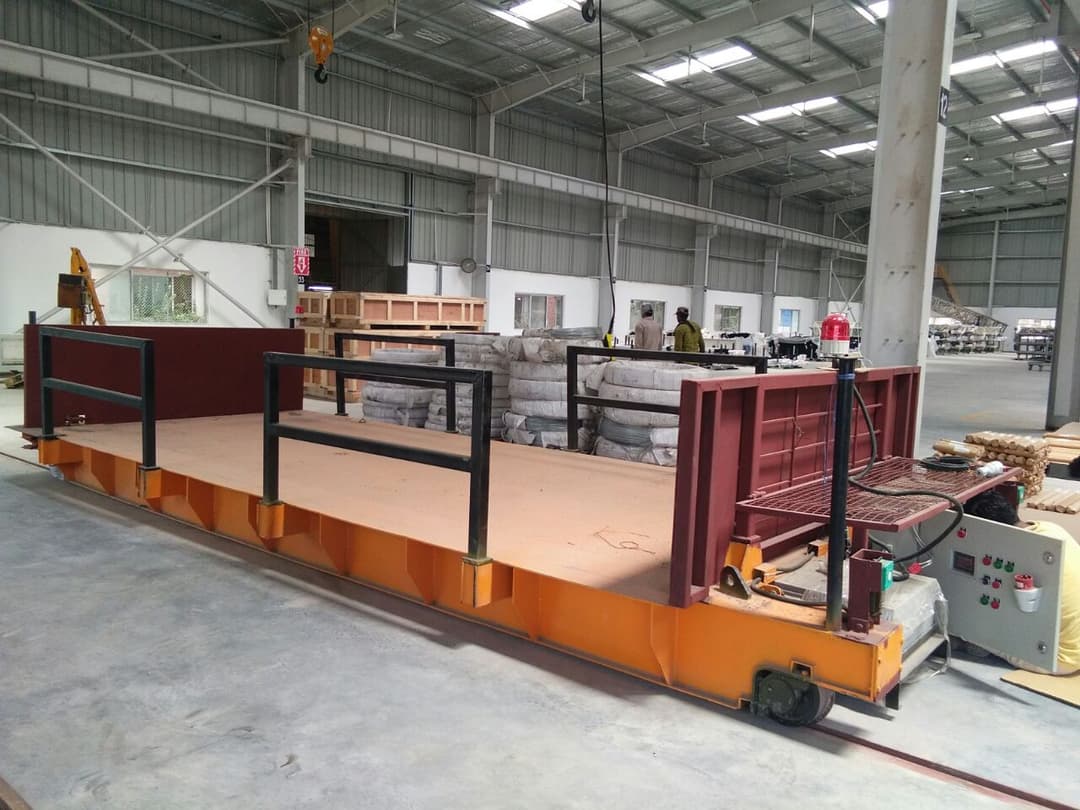
Motorised Trolly
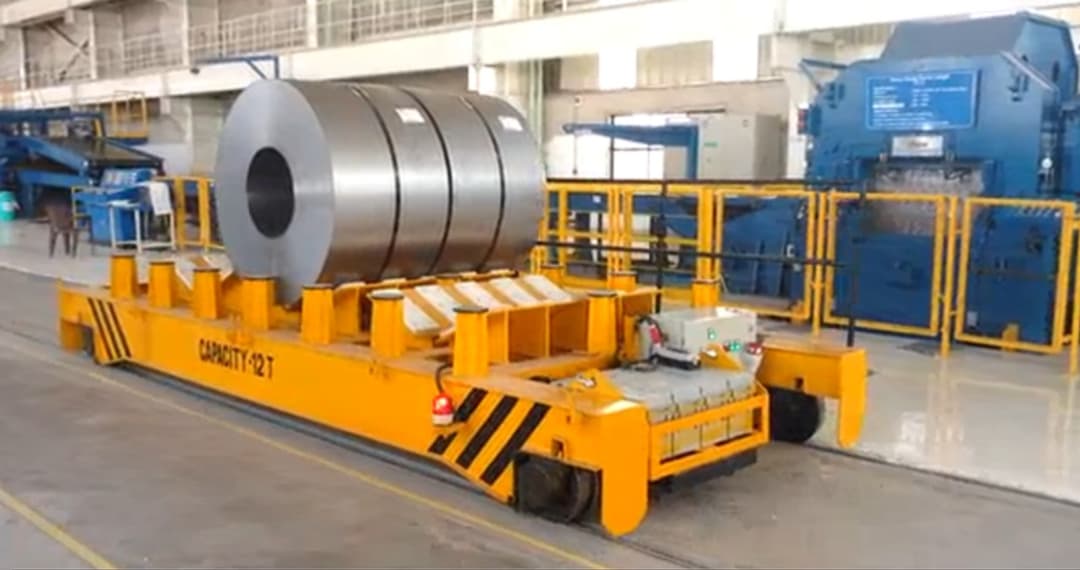
Motorised Trolley 12T
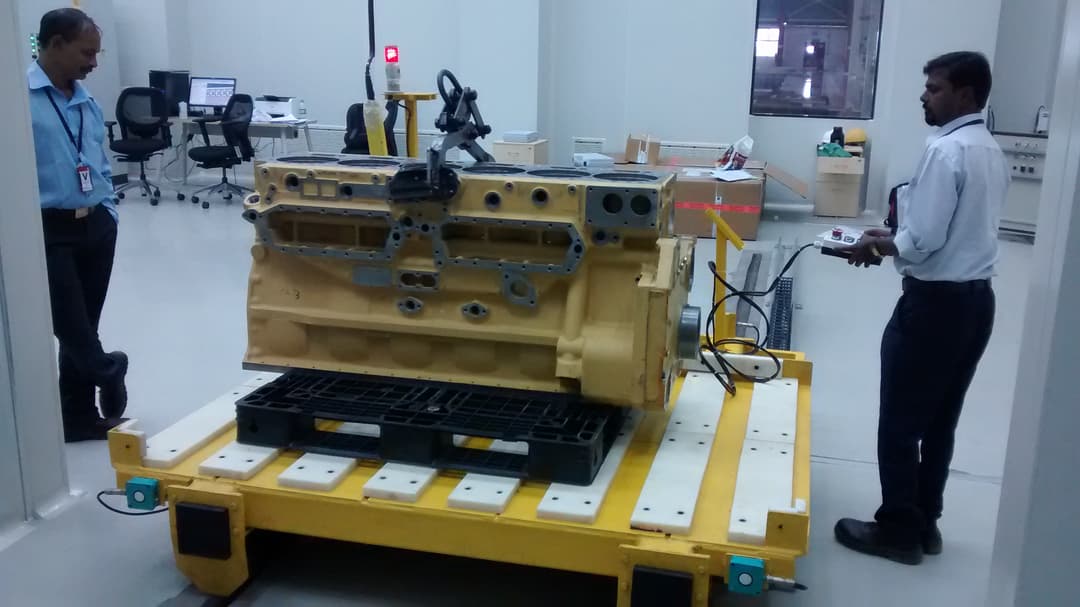
MRT DragChain
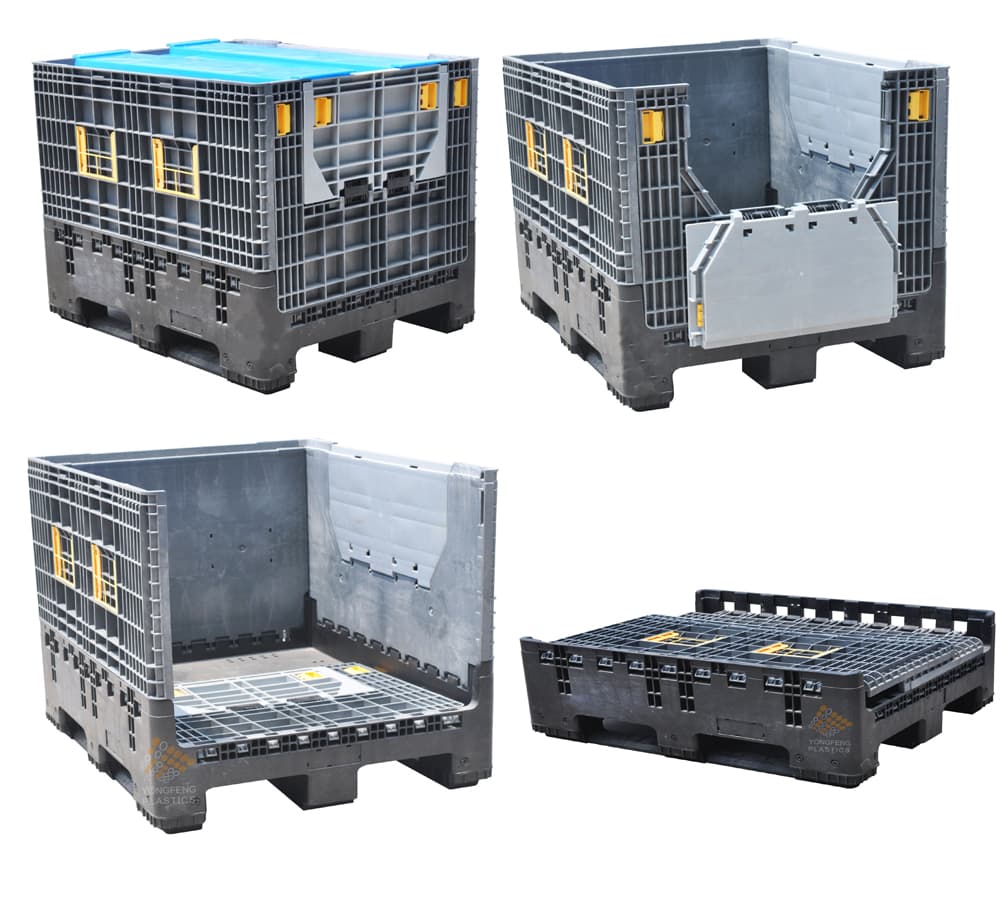
Pallet - Foldable
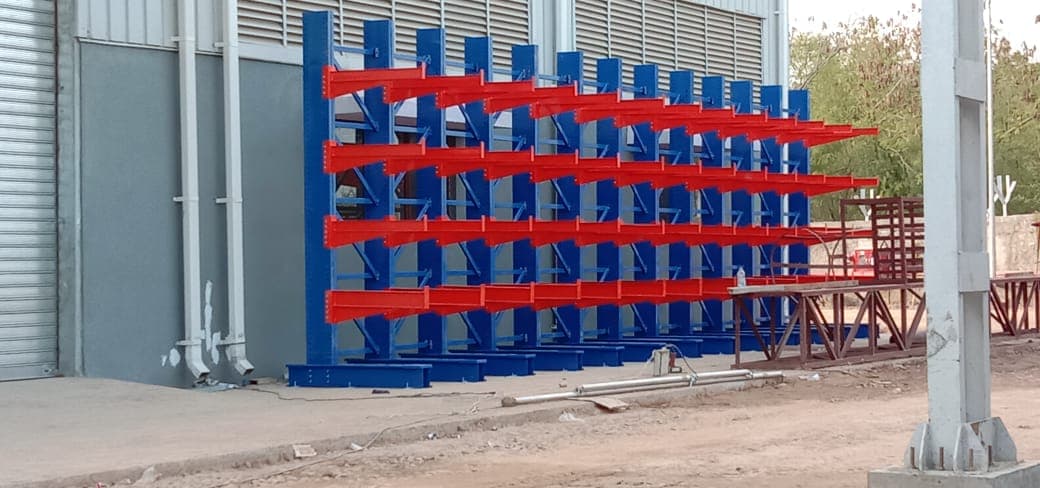
Rack - Cantilever
.1349a097.jpg&w=1080&q=75)
Rack - Cantilever
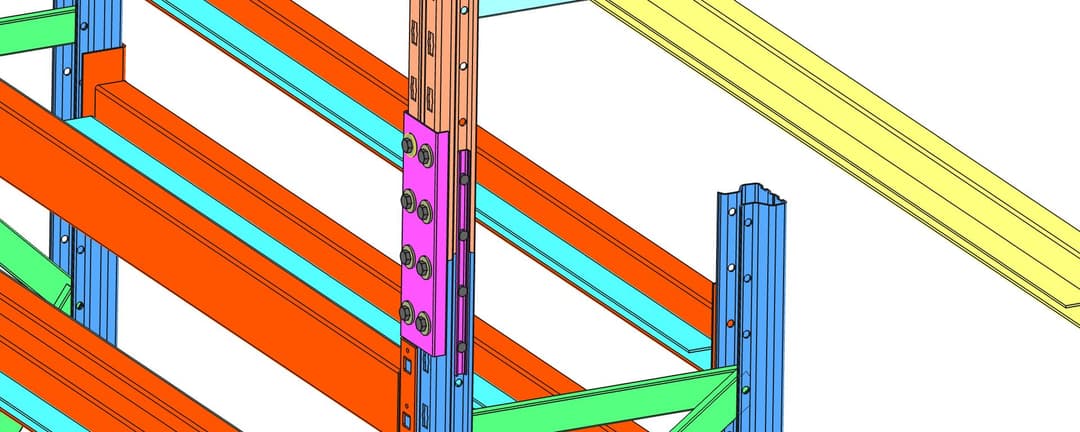
Rack - Modification
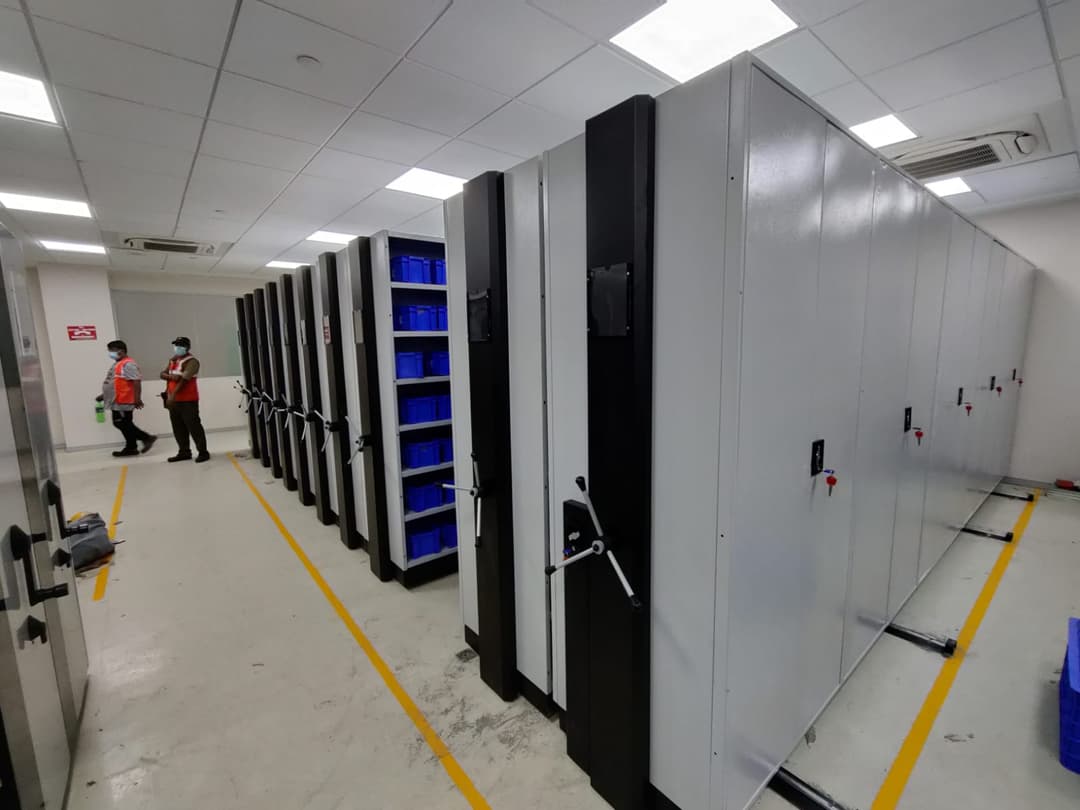
Rack - Compactor
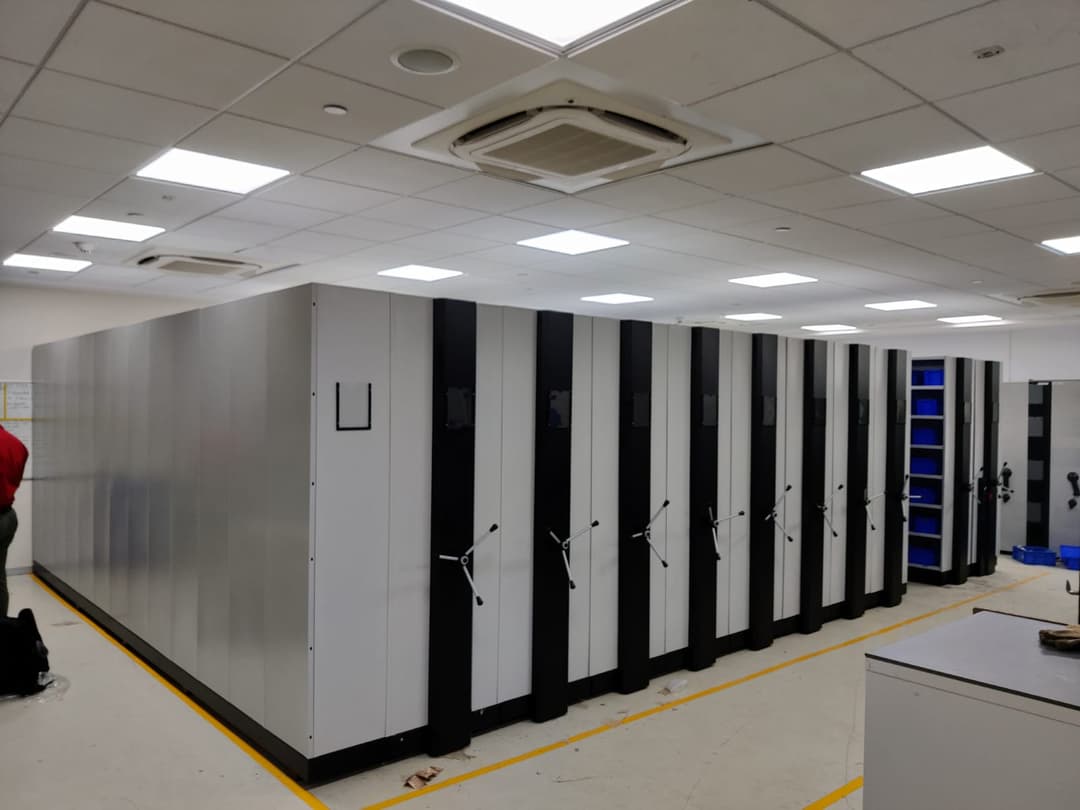
Rack - Compactor
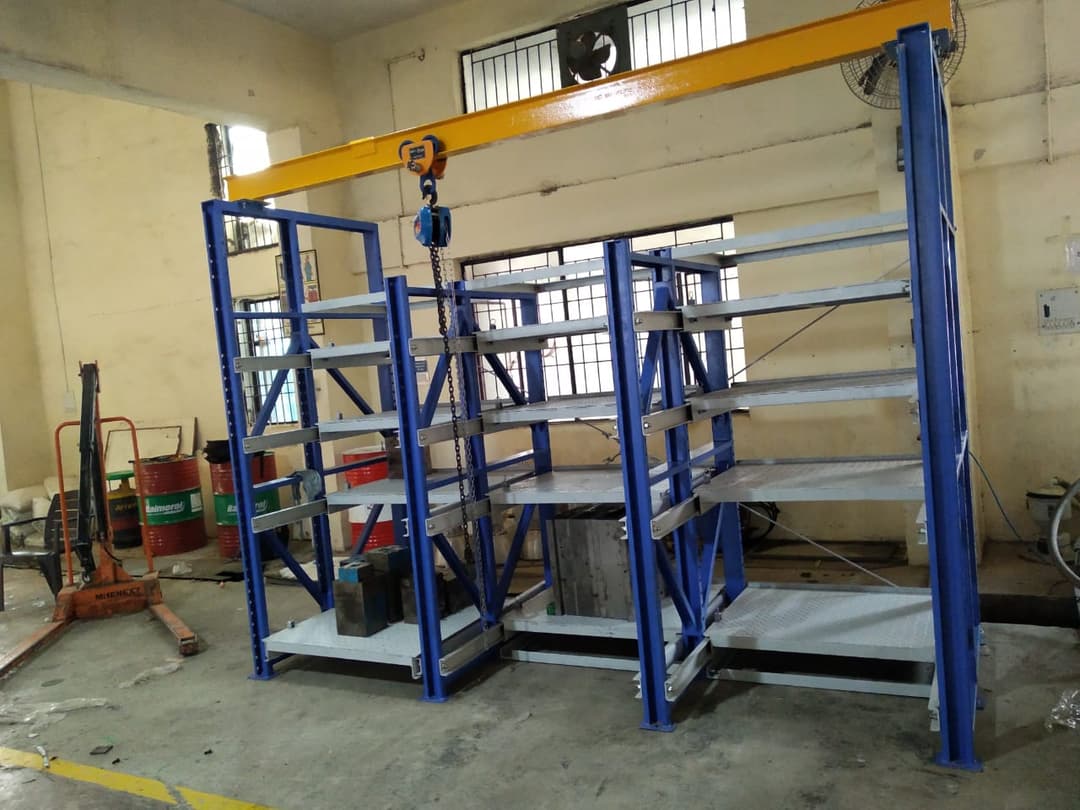
Rack - For Moulds
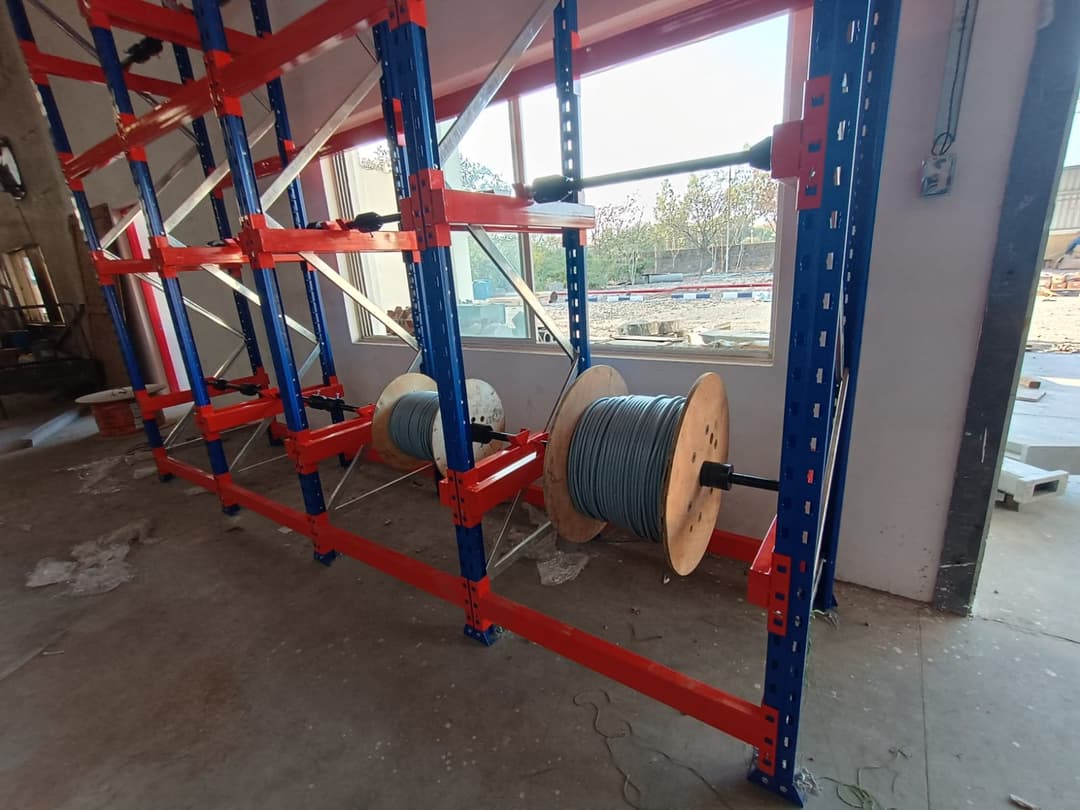
Cable Reel Rack
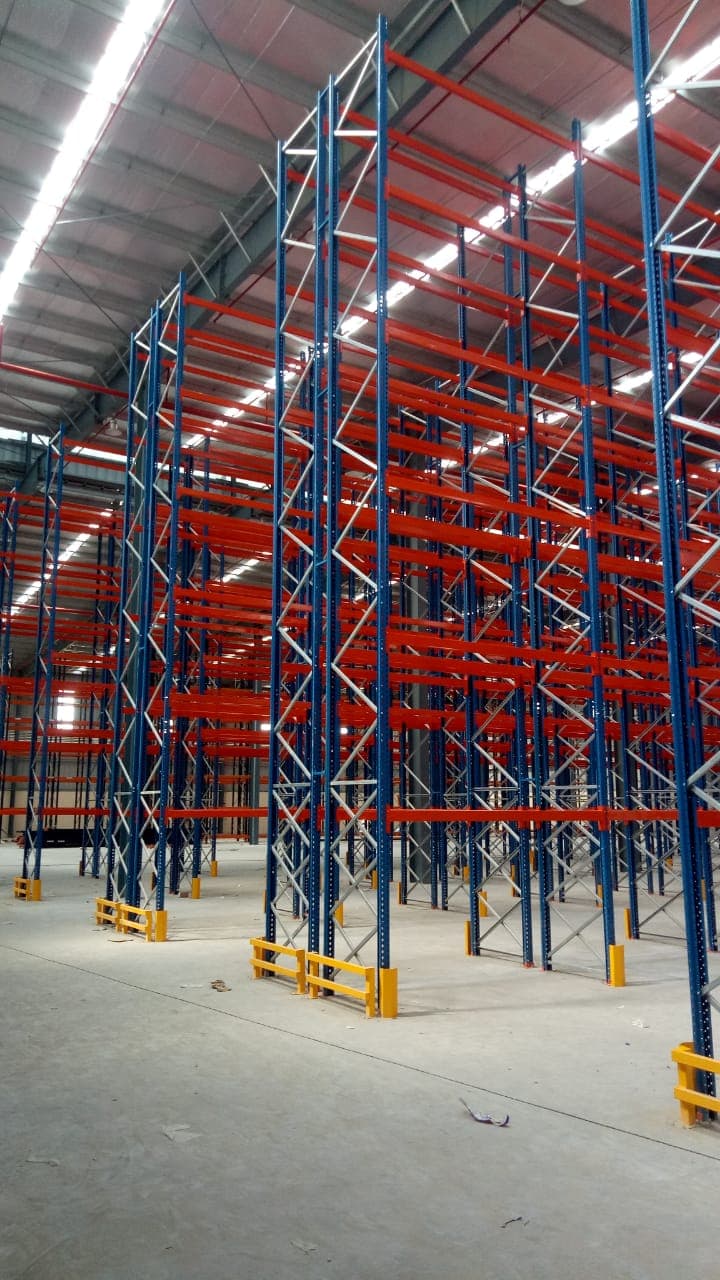
Racking System
.c13d927e.jpg&w=1080&q=75)
Racking System
.410271b2.png&w=1080&q=75)
Scissor Lift - Tilting
.376a0eff.jpg&w=1080&q=75)
Scissor Lift - Tilting
.eabc170c.jpg&w=1080&q=75)
Scissor Lift - Tilting
.5cdfe3cd.jpg&w=1080&q=75)
Scissor Lift - Tilting
.f642e3a2.jpg&w=1080&q=75)
Scissor Lift - Tilting
.98201bda.jpg&w=1080&q=75)
Scissor Lift MT
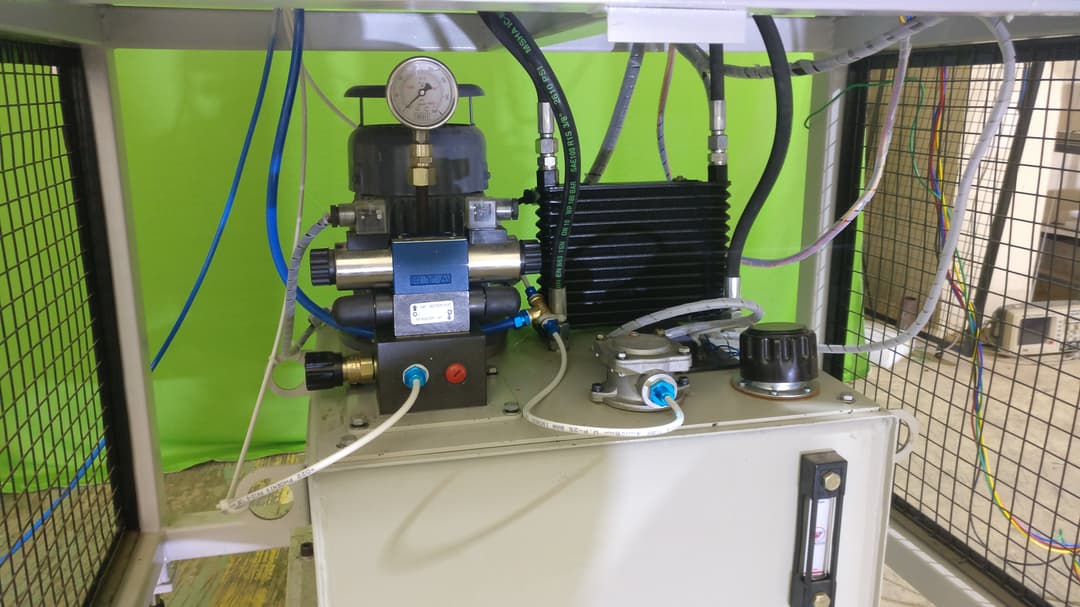
SPM Hydrolic
.38503b54.jpg&w=1080&q=75)
SPM - Injector
.b8b80edc.jpg&w=1080&q=75)
SPM - Rotary
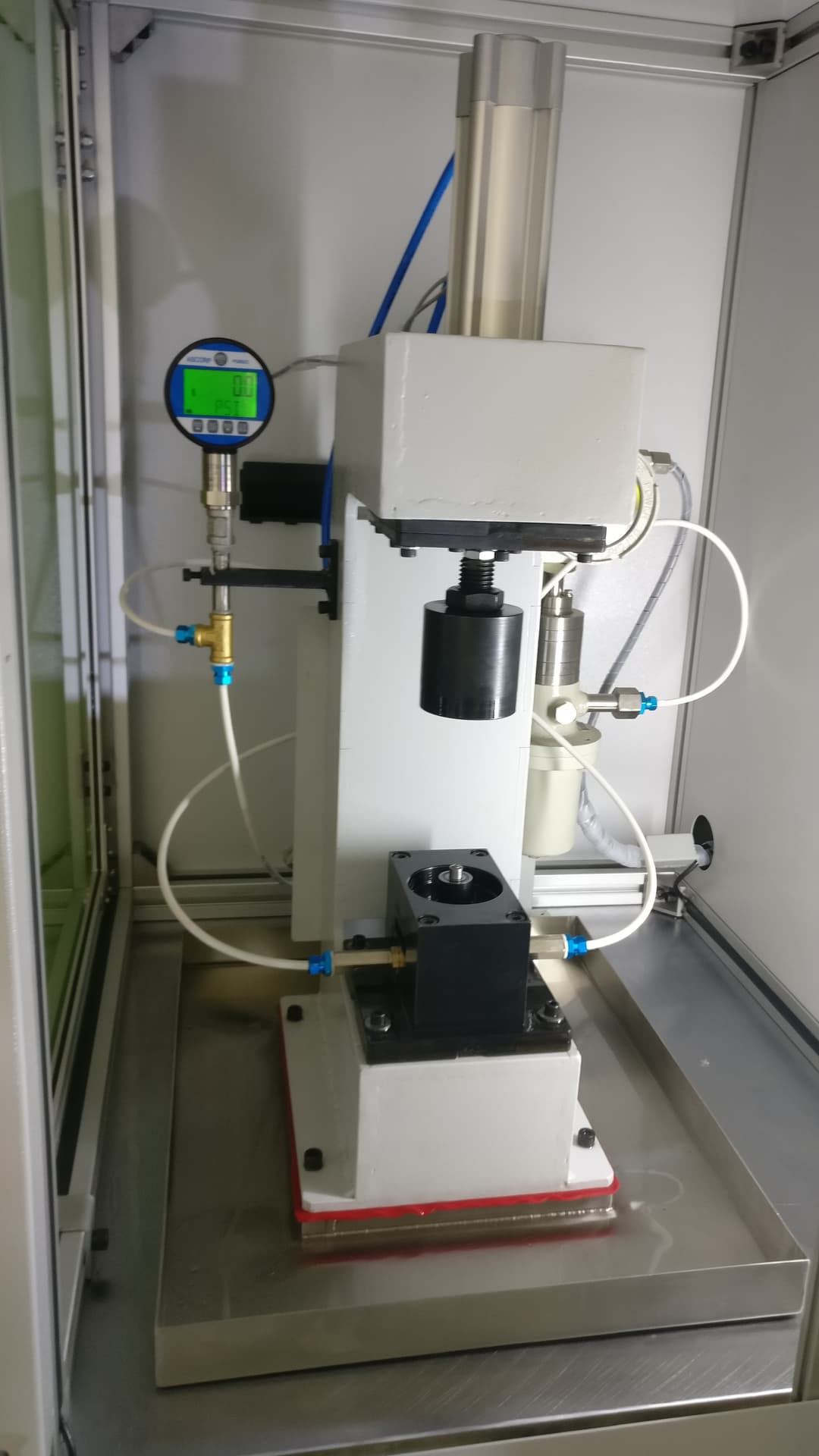
SPM
.594a9ffb.jpg&w=1080&q=75)
Work Table - Motorised
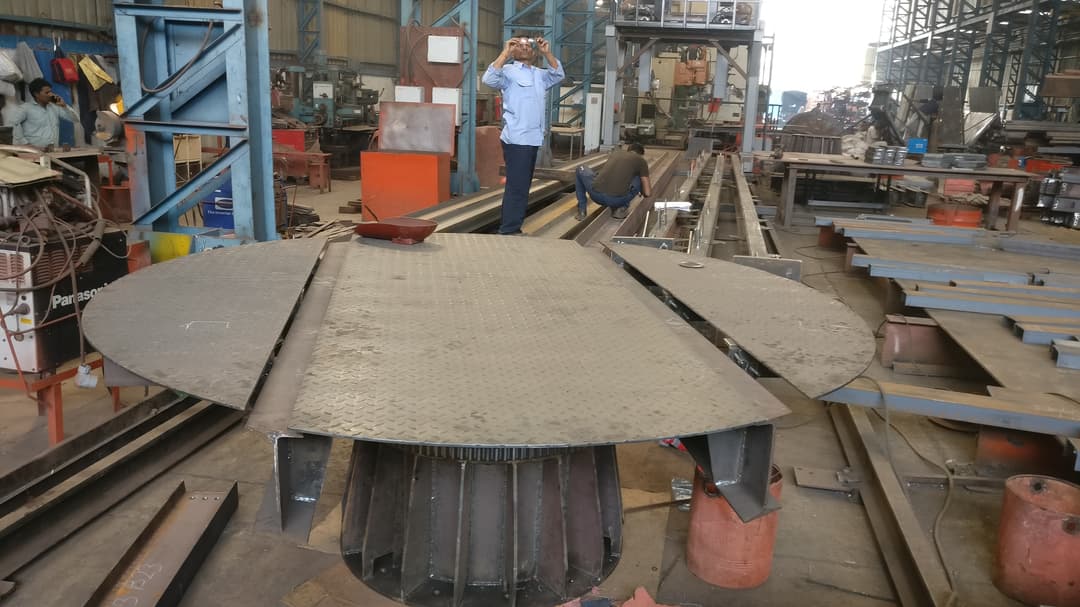